출처 : http://ss7893.blog.me/21096669
1. 개요
- 프로젝션용접(Projection welding
- 저항심용접(Resistance seam welding)
- 업셋용접 또는 저항벗용접(Upset welding or resistance butt welding)
- 플래시용접 또는 플래시벗용접(Flash welding or flash butt welding)
- 벗심용접(Butt seam welding)
상기의 저항용접법은 모든 경우에 저항발열을 주로 이용하여 용접하는 기법이라고 할 수 있다. 그 중에서도 가장 많이 적용되는 용접법이 점용접이다.
한편 자동차용 아연도금 강판의 도금층이 두꺼워지고 용접부에 오목자국이 없는 것이 요구되며, 금형과 프레스 기술이 발달함에 따라 프로젝션용접의 적용도 점차 확대되고 있는 추세이다. 또한 자동차 차제 조립에 적용되는 테일러드 블랭킹 공법의 핵심기술중에 하나인 머시심용접(Mash seam welding)도 관심의 대상이라고 할 수 있다.
2 저항용접의 원리
도체에 전류를 흐르게 하면 도체 내부의 전기 저항에 의하여 열 손실을 일으킨다. 일반적으로 전기회로에서는 이와 같은 손실을 최소화하는 방향으로 기술을 발전시키고 있으나, 저항용접은 발열 손실을 오히려 적극적으로 활용하는 용접기술이다.
즉, 저항용접이란 압력을 가한 상태에서 큰 전류를 흘려주어 금속끼리의 접촉면에서 생기는 접촉저항과 금속의 고유저항에 의하여 열을 얻고, 이로 인하여 금속이 가열 또는 용융하면 가해진 압력에 의하여 접합이 이루어 지도록 하는 공법을 말한다.
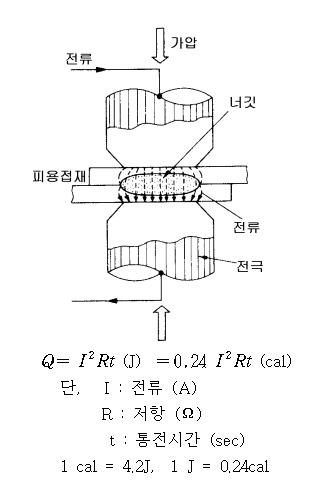
그림 4.1에는 저항용접의 원리
* 저항용접의 3대 요소는 다음과 같다.
(1) 가압력
(2) 전류
(3) 통전시간
3 저항발열의 원리
저항발열의 원리는 저항을 가진 금속에 전류가 흐를 때 발생하는 열량 즉 저항열(또는 줄열)Q에 의하며 상기와 같고저항발열량 Q는 아래와 같이 전류밀도의 항으로 표현할 수도 있다
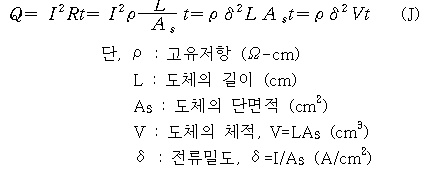
4 저항용접부 각부의 명칭
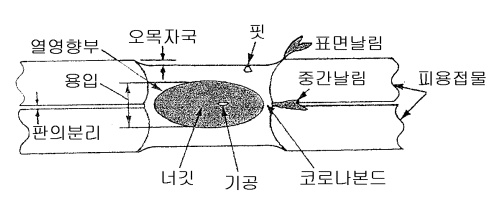
너깃(Nugget) : 용접결과로 접합부에 생기는 용융 응고한 부분으로서 일반적으로 접합면을 중심으로 바둑돌 모양으로 형성되어 있다.
코로나 본드(Corona bond) : 너깃 주위에 존재하는 링형상의 부분으로서 실제 용융하지는 않고 열과 압력을 받아서 고상으로 압접된 부분을 말한다. 이 부분은 접합부의 강도에는 기여하지 않고 비파괴 검사시에 너깃치수를 크게 평가하기 쉽게 하는 부분이므로 주의가 요구된다.
오목자국(Indentation) : 전극팁이 가압력으로 모재에 파고 들어가서 오목하게 된 부분을 말한다. 이와 같은 깊이를 오목깊이라고 한다.
용입(Penetration):피용접재가 녹아들어간 깊이로서 너깃의 한쪽 두께와 같다.
기공(Blow hole) : 너깃 내부에서 용융중에 발생한 기포가 응고시에 이탈하지 못하고 남아있는 공동을 말한다. 일반적으로 너깃의 중앙부에 발생하며 과대한 전류나 부족한 가압력으로 인하여 용융금속이 날아나간 자리에 형성된다.
중간날림(Expulsion) : 용융금속이 코로나 본드를 파괴하고 외부로 튀어나가면서 날리는 것을 말한다. 점용접이나 프로젝션용접에서 가장 해결하기 어려운 문제중의 하나라고 할 수 있다.
표면날림(Surface Flash) : 전극과 피용접재의 접촉면에서 피용접재나 전극이 용융해서 튀어나가는 것을 말한다. 중간날림보다는 자주 생기지 않지만 주로 점용접에서 도전률이 나쁜 전극소재를 사용하거나 냉각부족 또는 전극팁 직경이 과소한 경우에 자주 생기고 전극팁의 손상에 가장 큰 영향을 미친다. 한편, “Splash"는 중간날림과 표면날림을 포괄하는 일반적인 용어로 사용되고 있다.
오염(Pick up) : 전극과 피용접재의 접촉부가 과열되어 전극의 일부분이 피용접재에 부착하거나 전극과 피용접재 부분이 오염되는 현상을 말한다. 도금강판을 용접할 경우 도금층이 전극에 부착되어 이러한 현상이 자주 일어나므로 별도의 주의를 요한다.
5.스폿용접과 프로젝션용접의 비교
저항용접중 스폿용접과 프로젝션용접의 구분은 다음과 같다. 즉 전극팁의 형상에 의해서 전류밀도가 커지도록 되어 있으면 스폿용접이고, 피용접재의 형상에 의해 전류밀도가 크게 되어 있으면 프로젝션용접이라고 할 수 있다.
그림(a) (b)는 스폿용접과 프로젝션용접의 개념을 비교하여 나타낸 것으로서 스폿용접은 전류밀도를 높게 하여 발열량을 크게 하기 위하여 전극팁을 뾰족하게 유지하여야 한다. (b)의 프로젝션용접은 피용접재의 형상이 전류가 선택적으로 흘러서 전류밀도가 높게 될 수 있도록 준비되어 있으므로 전극팁의 형상이 뾰족하지 않아도 된다. 스폿용접과 프로젝션용접을 요약하여 비교하면 다음과 같다.
스폿용접 : 그림 (a)
- 전극의 형상과 가압에 의해서 전류 통로가 제한적으로 형성
(전류밀도를 높이기 위해 뾰족한 전극팁 형상과 가압을 이용)
- 저항열은 전극사이의 좁은 전류 통로에서 발생하여 접촉부를 용융
프로젝션용접 : 그림 (b)
- 피용접재의 돌기와 가압에 의해서 전류 통로가 제한적으로 형성
(전류밀도를 높이기 위해 피용접재의 돌기부와 가압을 이용)
- 저항열은 돌기부와 그 상대 피용접재의 제한된 전류 통로에서 발생하여 접촉부를 용융(돌기부가 먼저 녹는 것이 일반적 현상)
그러나 원형 단면을 가진 피용접재와 판재를 용접하는 경우에는 스폿용접과 프로젝션용접의 중간 상태라고 할 수 있다. 즉 전극팁의 크기가 너무 커서는 전류밀도가 낮아져서 용접하기가 곤란하고 전극팁의 크기가 너무 작아서는 과열하기 쉬워서 전극의 소모가 심하게 된다. 따라서 전극팁의 크기는 적절하게 허용범위를 가져야 하며, 용접중 전극팁의 크기가 변하면 품질에 영향을 미치게 되므로 주의를 요한다.
6점용접 전극의 종류
(1) 점용접 전극의 역할과 손상
점용접시 전극의 역할은 다음과 같이 요약할 수 있다.
● 가압의 역할
● 통전의 역할
● 냉각의 역할
● 부품을 고정하는 역할
점용접 전극으로서 갖추어야 할 기본적인 요구조건은 다음과 같다.
● 고유저항이 작아서 통전시 발열이 작게 될 것.
● 용접시의 피용접재와 전극 접촉면에서 열량을 잘 흡수할 것.
● 고온에서 경도와 강도가 높고, 연속 사용에 의한 마모와 변형이 작을 것.
한편, 전극의 적절한 형상으로서 고려해야 할 사항은 다음과 같다.
● 교환이 용이할 것.
● 직경 및 선단 형상이 적절할 것.
● 냉각 방식이 적절하여 선단의 과열로 인한 지나친 마모와 변형을 억제할 수 있을 것.
점용접용 전극의 손상의 원인
고온 마모와 변형 : 전극 고유저항에 의한 발열, 전극과 피용접재 표면 사이의 발열, 너깃으로부터의 열전도 등에 의하여 전극 선단의 온도가 상승하여 마모나 변형이 쉽게 일어나는 것. 전극선단의 고온문제는 냉각방식, 전극선단의 형상, 피용접재의 재질과 표면상태, 용접조건(전류, 통전시간, 가압력) 및 단위시간당의 용접횟수 등에 크게 좌우된다.
전기적 손실 : 용접부의 표면상태가 나빠서 국부적으로 통전하여 국부 가열 되거나, 가압력이 부족하여 국부 통전 및 국부 과열하여 전극이 부분적으로 손상되거나 표면날림이 생기면서 손상되는 것.
화학적 손실 : 산화물이나 표면처리 물질이 전극 선단에 부착하거나, 가압력과 고온으로 인하여 재료의 일부가 전극으로 확산하게 된다. 이에 따라 전극 표면이 합금화되어 전기전도도와 열전도도가 저하하면서 전극 선단의 온도가 과도하게 상승하여 손상을 입는 것.
(2) 전극 재료와 형상에 관한 규격
1) 점용접 전극 재료에 관한 규격
점용접시의 전극 선단은 400-500℃로 가열되고, 압축응력도 4-20kg/mm2로 상당히 높으며, 높은 전류를 흘려주어야 하는 가혹한 상태에 놓이게 된다.
전극의 선단중심부가 과열하여 연화한 부분을 나타낸다. 전극 선단의 중심부가 과열되어 연화되지만, 주위의 비교적 저온인 부분이 연화하지 않고 높은 경도와강도을 가지고 있으므로 중앙부의 국부적인 변형이 억제된다.
점용접용 재료는 크게 다음과 같이 3종류로 구분된다.
① Group A : 동계 합금으로서 Class 1 - Class 5 로 세분
② Group B : 텅스텐과 동의 소결합금으로서 Class 10 - Class 13으로 세분
③ Group C : 특수합금
Cu-Cr계 합금
적당한 열처리를 행한 Cr 0.5-1.0%를 포함하는 동합금은 전기전도도와 기계적 성질이 우수하다.
Cu-Ag계 합금
합금은 냉간가공에 의해 “HRB 60"이 된다.
Cu-Zr계 합금(Cu0Zirconium)
5% 이하의 Zr을 포함한 동합금은 시효처리에 의해 기계적 성질과 전기전도도를 현저하게 개선하는 것이 가능하다.
Cu-Be계 합금
Cu-Be 합금은 시효경화성 합금으로 높은 전도성을 갖는 것은 적당한 열처리에 의해 전기전도도 25-60%(I.A.S.C), 인장강도 80kg/mm2에 달한다
크롬합금동의 취급시 주의 사항
합금동의 특징을 충분히 발휘하여 사용하기 위해서는 아래사항을 주의햐한다.
① 고온 500℃ 이상의 장시간 연속사용은 가능하나 그 이상의 온도로 사용하면 내열성이 우수하다고는 하나 기계적 성질이 열화해서 수명이 단축된다. 또한 전극을 설계하는 경우 냉각에 주의하여 500℃ 이하까지 냉각을 잘하면 수명연장 효과가 있다.
② 가열하여 가공하면 전극재의 특성이 급격히 저하되므로 주의해야 한다.
7저항용접기의 종류
(1) 저항 용접기의 기본 구성
저항 용접 방법은, 저항 발열을 이용하여 금속 재료를 용접하는 방법의 일종이다. 통상은 그림과 같이, 수냉 동전극으로 용접부를 상하로 가압하여, 이 상하 전극간에 집중하여 흐르는 1초 이내의 극히 단시간 전류에 의한 집중 발열(Joul열)로 판 표면과 뒷면의 전극에 의한 냉각 작용을 이용하여 접합부만을 용융시켜, 이곳에 용접 너깃(Nugget)을 생성시킨다.
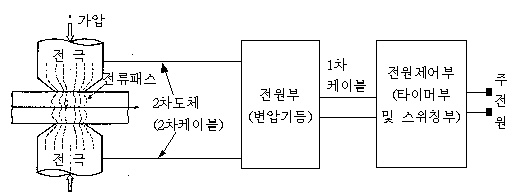
발열원으로 줄열을 이용하는 점에 있어서는, 니크롬선을 이용한 일반의 전기 난로나 전기 다리미의 경우와는 별로 다른 것은 아니나, 보통 양자의 저항치 크기에는 큰 차이가 있다. 니크롬선의 저항치가 통상 10Ω정도인데 비해, 저항 용접부의 저항치는 극히 적은, 겨우 100μΩ(10-4
Ω)정도밖에 되지 않는다. 이 때문에 저항 용접부에 충분히 집중 가열을 하여 양호한 용접부를 만들기 때문에 수천~수만A라는 대전류를 필요로 한다. 그리고, 이 대전류를 공급하는 문제로 저항 용접기의 2차 케이블(용접 케이블)이 결국 커지므로, 전극을 고정하는 가압부도 강성이 높은 것이 요구된다.
또 저항 용접시 전압은 팁간 전압에서 1 ~ 2V정도, 전극 팁부, 2차 케이블부를 포함해도 겨우 10V정도밖에 되지 않는다. 이 때문에 용접에 필요한 대전류를 효율적으로 공급하기 위해 용접부와 주전원(공급 전압 220V또는 440V)간에는 적당한 변압기가 삽입된다. 통상, 이 변압기의 2차 전압은 수V ~ 20수V로 설정되고 있다. 그리고 용접 전류치와 통전시간등은 전류치가 작은 1차 측에서 제어되는 것이 일반적이다.
(2) 저항 용접기의 구조적 형태에 의한 분류
저항 용접기는 변압기와 가압 장치등 각부를 구조적으로 조합하는 방법에 의해 다음 같이 분류할 수 있다.
저항용접부 -- 정치형
포터블형 : 분리형과 일체형(변압기)
1) 정치형 저항 용접기
정치형은 그림에 나타내는 바와 같이, 각부를 전부 일체화하고 가압 장치와 전원 장치를 고정하여 두는 형으로, 범용기로서 이용되고 있다. 자동차 제조 이외에도 박판의 조립 현장에서는 상당히 널리 이용되고 있다.
그림에서 볼 수 있는 바와 같이 가압용 에어 실린더가 상부에 위치해 있어서 가압 및 용접시 수직 하강 운동을 함으로서 용접시 전극의 추종성을 우수하게 하고 있다.
2) 포터블형 저항 용접기
그림에는 자동차 제조 공장 등에서 가장 많이 이용되고 있는 건·변압기 분리형 포터블 저항 용접기의 예이다.
저항 용접기 전체는, 가압통전부(건부)와 전원부(변압기부), 전력제어부(타이머·콘덕터부), 및 1차 케이블과 2차 케이블부(2차 도체부)로 나누어진다. 가압·통전부는 건프레임과 가압실린더, 전극홀더, 전극 및 기동 스위치로 구성된다. 전원부는 용접 변압기와 가압실린더 제어용 공압기기, 냉각수의 입구 등에서 전력제어부는 통전시간과 용접전류치 등을 설정하기 때문에 타이머부와 이것을 직접 제어하는 대전류 스위칭소자로 구성된다.변압기 부착 건타입은, 그림에서의 가압·통전부와 전원부를 일체화하여 구성한 것으로, 기본적으로는 그림와 같은 형이 있다. 일체화하는 것에 의해 소모품의 2차 케이블 레스화가 도모되고 있다.
8.용접부의 품질 관리
(1) 용접품질의 평가
요구되는 용접품질은 그 용접부의 적용 대상이 무엇이냐에 따라서 달라진다. 일반적으로 점용접, 심용접, 돌기용접의 용접품질은 용접부가 가져야 할 표면 형상, 용융부 크기, 기계적 성질, 내부 결함 및 용접 후 피용접재의 분리와 날림 발생 등을 기초로 결정한다.
용접부의 성능을 측정하기 위한 확실한 비파괴 검사법은 아직 개발되지 않았으므로, 기존의 규격에서는 파괴 시험에 의한 용접부의 기계적 강도 측정, 또는 미세 조직을 확인하고 그 결과를 이용하여 용접부의 품질을 평가하는 것이 대부분을 차지하고 있다. 그러나, 미세 조직 시험과 용접부 인장 전단 시험만으로는 용접부의 품질을 종합적으로 판정하는데 한계가 있으므로 설계자는 이러한 점을 고려해야 한다. 용접부의 품질 검사를 위한 방법을 열거하면 다음과 같다.
1) 용접부 외관
일반적으로 점, 심, 돌기 용접부의 외관 품질을 판정하기 위한 근본적 관심은 비슷하다. 즉, 표면 날림, 전극으로부터의 오염, 기공, 균열 및 압흔 등이 주요 판정 항목이며 이들은 용접부의 품질에 치명적인 영향을 미치기도 한다.
2) 너깃의 크기
너깃의 직경은 설계 사양과 관련되는 것이며 일반적인 용접조건으로 용접된 점 용접부의 경우는 얇은 쪽 소재 두께의 3.5-4배에 해당하는 너깃 직경이 있어야 한다. 그 밖에도 다음과 같은 사항들이 검토의 대상으로 알려지고 있다. 즉, 용기 제조에 있어서 사용 중 내용물의 누설 방지를 위한 심 용접 너깃은 적어도 25%이상의 용접부 겹침이 있어야 한다. 또, 너깃의 직경은 이종 두께의 소재를 용접 할 경우 얇은 쪽 소재 두께의 3.5-4배는 되어야 한다. 한편, 돌기 용접부는 용접 전 성형된 돌기의 직경보다 같거나 큰 너깃을 가져야 한다.
3) 너깃 두께
너깃 두께는 피용접 모재 두께에 대한 용접부의 두께를 의미한다. 저항 용접에서 최소 너깃 두께는 모재 두께의 20%이상 되어야 하는 것으로 알려져 있다. 너깃 두께가 20%보다 적을 경우에는 용접에 사용된 입열에너지의 총량이 부족하였다고 판단할 수 있다. 또, 너깃의 최대 두께는 모재 두께의 80%미만이어야 한다. 너깃 두께가 지나치게 큰 조건으로 용접이 이루어지면 용접 과정에서 날림의 발생과 심한 압흔의 생성으로 용접품질을 떨어뜨리고 전극의 마모를 촉진하여 작업성을 해친다.
4) 용접부의 기계적 성질
점, 심 및 돌기 용접으로 결합된 구조물은 인장 또는 압축 하중이 작용할 때, 용접부에 전단 하중이 주로 작용할 수 있도록 용접 설계가 이루어 진다. 그러나, 실제로는 용접부에 인장 전단 하중이 동시에 작용하는 경우가 더 많기 때문에 이러한 조건도 검토가 이루어져야 한다. 이러한 특성을 평가하기 위하여는 규격이 정하는 인장 전단 시험을 포함하여 십자형 인장 시험 또는 용접부 피로 시험을 실시한다. 점 용접에서 용접부의 연성을 평가하기 위한 방법은 인장 전단 강도값과 십자형 인장 강도값을 구한 다음에 그 비를 계산하는 것으로 이 값을 연성비라고 부른다. 연성비는 특히 고장력 박판 강재의 용접부 특성을 판단하는 지표가 되기도 한다. 참고로 겹침 저항용접부의 시험에 대해 나타낸다.
(2) 용접품질의 감시방법
저항용접 공정의 용접품질 감시 방법은 직접적인 방법과 간접적인 방법으로 나뉘어진다. 직접적인 방법은 집속형 초음파 탐상법 등을 이용하여 너깃의 생성을 직접 감시하는 방법이다.
탐촉자의 설치 장소, 계측 결과의 신뢰성이 문제시 되어 상용화까지는 다소의 시간이 더 필요한 기술이다. 간접적인 방법은 용접 공정 변수를 이용하여 용접부의 품질을 예측하는 방법과 용접 현상을 직접 측정하여 그 결과와 용접품질을 연계시키는 방법이 있다. 생산 공정에서는 후자 보다는 전자의 경우가 더 효과적이라고 할 수 있는데, 그 이유는 각각의 용접 조건과 그 때의 용접부 품질을 미리 설정하고 그 설정 범위에서 용접이 이루어지게 하는 것이 현장의 관리상 유리한 점이 더 많기 때문이다. 그러나, 용접부의 온도를 계측하고 그 결과를 품질 감시 요소로 이용하는 것, 점 용접의 경우에 자주 거론되는 용접 과정에서의 동 저항 및 전극 이동 현상을 이용하는 방법 등이 대표적인 용접 품질의 감시 방법이라고 할 수 있다. 여기에서는 점 용접부의 동 저항 변화와 용접시 발생하는 소재의 팽창-수축을 품질 감시 요소로 이용하는 방법을 개략적으로 기술한다.
1) 동 저항(Dynamic resistance)
용접 과정을 정성적으로 보여주는 현상인 동 저항은 용접 도중 전극 양단의 전압 강하와 용접 전류를 이용하여 계산할 수 있다. 아래그림은 용접 도중 변화하는 동 저항값을 얻기 위한 측정장치의 개략도이다.
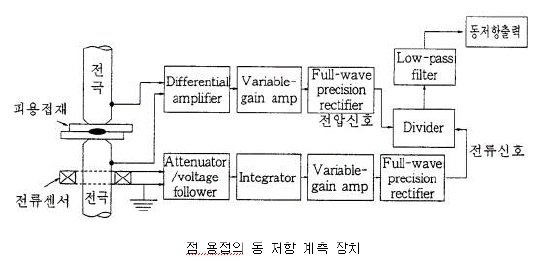
▶ 구간 Ⅰ : 용접 초기의 현상으로 수ms의 시간 내에 발생하는 동 저항의 변화를 보여주고 있다.
▶ 구간 Ⅱ : 용접전류가 흐르기 시작하여 온도가 상승하면 소재의 강도 하락으로 전극과 소재 사이의 접촉 면적이 증가하는 구간이다.
이 때, 표면의 접촉저항은 감소하지만 온도상승에 의한 피용접재의 고유 저항이 증가하여 이들이 서로 복합적인 효과를 나타내며 평형을 이루는 점(a)이 나타난다. a점의 동 저항은 용접 과정에서 최소값을 보이지만, 이 점을 지나면서 온도 상승에 의한 저항 증가와 효과가 접촉 면적 증가에 의한 저항의 감소 효과를 상쇄시키면서 동 저항은 증가하기 시작한다.
▶ 구간 Ⅲ : 동 저항은 온도 상승과 더불어 계속 상승하다가 이 구간이 끝나는 부근에서 피용접재의 접촉면은 부분적인 용융을 일으킨다.
▶ 구간 Ⅳ : 다음과 같이 몇가지 상반되는 현상이 발생한다. 피용접재의 온도는 계속 상승하여 총 저항을 증가시켜 동 저항도 증가한다. 용접이 진행됨에 따라 계속적으로 발생되는 열은 접촉 표면에서의 용융된 부분을 증가시켜 통전 단면적을 넓히기 때문에 저항의 감소를 초래한다. 온도 상승은 피용접재의 강도 하락을 유발하여 용접 가압력에 의한 전극간의 통전길이를 짧게 하기 때문에 총 저항도 낮아진다.
▶ 구간 Ⅴ : 피용접재의 접촉부에서 용융부가 계속 성장하면서 접촉면적이 넓어지기 때문에 동 저항도 감소한다. 만일, 용접 전류가 너무 큰 조건에서 용접을 실시하면 용융부도 짧은 시간에 급격히 많아지면서 주위의 고체 상태인 소재 금속이 전극 가압력을 더 이상 지탱하지 못하게 되고 용융 금속이 분출하는 날림 현상을 일으키며 동 저항 또한 급격히 감소한다
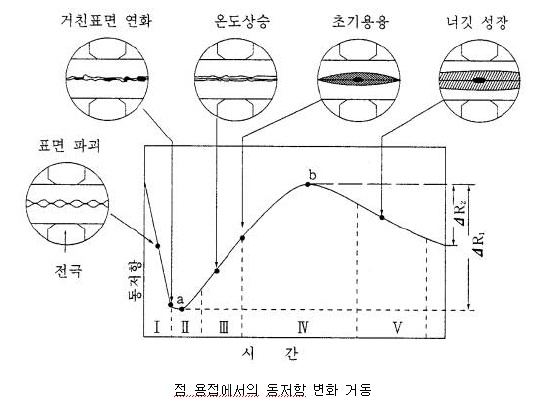
9.전기적 에너지를 이용한 가압 용접법
1.스폿(spot) 및 프로젝션(projection) 용접
스폿 용접과 프로젝션 용접은 둘다 용접개소에서의 주울(Joule)발열을 이용하여 접합면을 용융 또는 고온상태까지 도달하도록 하여 가압, 접합하는 방법으로서 판재의 접합에 주로 이용된다.
<그림1>은 스폿 용접의 원리를 나타낸 것이다. 용접 재료를 그림과 같이 겹쳐 놓고 수냉된 동 또는 동합금의 전극으로 물리게 되어있다. 전극 간에 순간적으로 대전류를 흐르게 하면, 전극의 접촉면과 판과 판의 접촉면 사이에서 저항열을 발생된다. 이때 전극과 판사이의 열은 전극 내부의 냉각수에 의해서 냉각되고 판과 판의 접촉면은 용융상태에 도달하게 된다. 이때 가압에 의하여 너깃(nugget)이 형성된다.
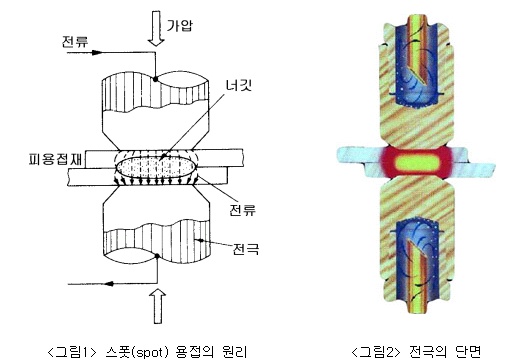
<그림3>은 프로젝션 용접의 원리를 나타낸 것이다. 한쪽 피용접재에 돌기(projection)을 만들고 그 부분을 평탄한 동전극으로 가압하면서 큰 전류를 흘려서 너깃을 형성시켜 접합하는 공법이다. 프로젝션이 만들어진 쪽에 오목자국이 형성되지 않는 것이 장점이다.
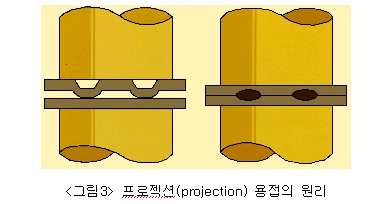
시임(seam) 용접
아래의 그림과 같이 원판 전극을 사용하여 용접전류를 공급하면서 가압 회전시켜 spot 용접을 연속적으로 행하면 선용접인 seam 용접이 된다. 이 때 공급되는 전류의 일부는 용접부로 흘러 손실되고, 일부는 원판 전극 사이에 흐르므로 대전류를 요한다.
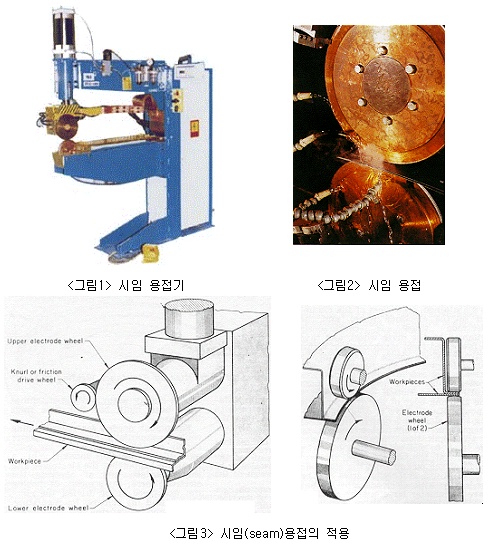
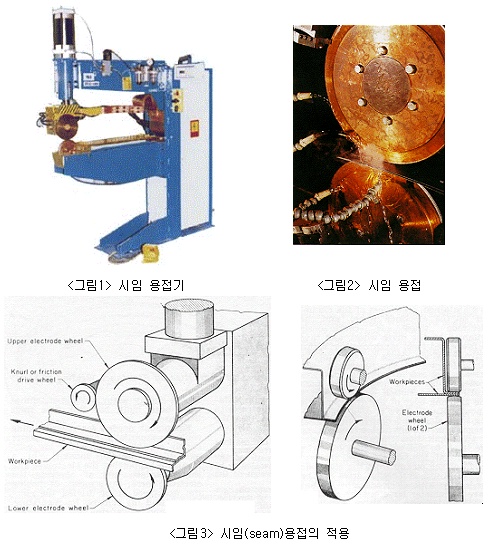
벗(butt) 및 플레시 벗(flash butt) 용접
전기 저항열을 이용하여 압접하는 방법으로 벗용접(resistance butt welding), 업셋용접(upset welding), 플래시 벗 용접(flash butt)이 있다.
벗(butt)용접법은 용접하려는 재료의 단면을 맞대어 전극 사이에 대전류를 통하면 양 재료 사이의 접촉저항에 의해 단면은 가열 연화한다. 이 상태에서 이동 전극측을 가압하여 용접한다.
플레시 벗(flash butt) 용접법은 저항가열 외에 아크열도 적극적으로 이용하여 비교적 넓은 접합 단면적을 가는 재료를 상대적으로 낮은 전류밀도를 적용하여 압접하는 방법이다. 보통 용접과정은 예열과정, 플래시 과정, 업셋과정의 3단계로 구성된다.
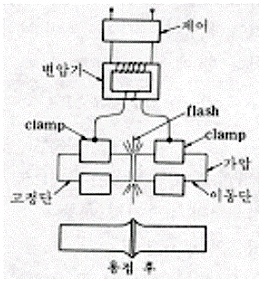
스터드(stud) 용접 및 퍼커션(percussion) 용접
스터드(stud) 용접 및 퍼커션(percussion) 용접은 둘 다 접합부에 직접 단시간의 아크를 발생시켜 국소적으로 용융시켜 가압, 접합하는 방법이다.
스터드 용접법은 봉재, 볼트 등의 스터드를 판 또는 프레임 등에 직접 심는 능률적인 용접법으로서 널리 채용되고 있다. 용접건에 스터드를 고정하고, 선단에 페룰(ferrule)이라고 하는 원통을 통해 모재에 접촉시켜 놓는다. 통전개시와 더불어 건 안의 스터드 상승기구에 의해 스터드가 모재와 떨어져 아크가 발생한다. 그 시간은 봉 선단 및 모재의 적정 용융이 달성되는 시간을 미리 구해 놓고 타이머에 설정해 둔다. 시한 종료와 함께 스터드를 용융풀에 눌러 붙이면 용접이 완료된다. 페룰은 아크 공간을 외계와 차단하여 아크 분위기의 보호 역할을 한다.
퍼커션 용접은 선봉 내지 같은 선재끼리, 또는 대형물품에 서제를 심는 용접에 이용되나, 현재로서는 용접의 안정성에 다소 문제가 있어, 공업적으로 사용되는 상태에는 도달해 있지 않다. 이 방법의 특징은 대전류의 아크를 극히 단시간 발생시키는 것이다. 이 때문에 용접법으로서는 아크 용접법에 가까운 스터드 용접법과 저항 용접법의 일부로 취급하는 플래시 용접법의 중간위치에 있다고 할 수 있다.
퍼커션 용접의 원리는 정류기를 거쳐 콘덴서에 축적한 에너지를 비교적 약한 가압력으로 눌러 접합개소를 통해 급속히 방전시킨다. 접합개소는 돌기부를 형성하고 있어 전류통로를 제한하여 이 부분을 용융시켜 대전류 아크를 발생시킨다. 이 아크 전류는 컨덴서 방전의 성격상 급격히 저감하고, 한편에서는 이 접합제에 가압력이 작용하기 때문에 한참 뒤에는 아크에 의한 용융부는 융합, 압착하여 용접이 완료된다. 가압에는 스프링 등에 의한 충격가압외에 자중(自重)에 의한 자연낙하를 이용하는 간단한 방식이 채용된다.
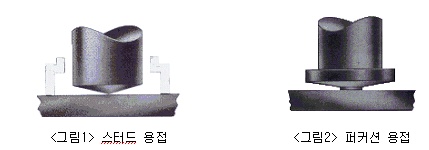
10. 기계적 및 화학적 에너지를 이용한 용접법
마찰 용접
(1) 원리와 용접방식
* 마찰용접 : 두 재료에 가압력을 가하면서 접합 표면을 서로 마찰하도록 하여 그 때 발생하는 마찰열을 이용하여 두 모재가 접합되도록 하는 공법.
1) Brake식 마찰 용접법 : 회전수, 가압력, 업셋량(Upset) 또는 가열시간
2) Fly wheel식 : 가압력, Fly wheel모멘트(원판) I, 회전수 n
관성 에너지 E = Iω2
/2 = I(2πn)2
/2 = 2π2
In2
여기서, 관성모멘트 I = mR2
/2, ω : 각속도(rad/sec), n : 회전수
(2) 용접조건
* 가압력 P1=2-8kgf/mm2
, Upset압력 P2=P1 또는 (2-4)P1, 주로 P2>P1
* 접합부에 금속간화합물이 생기는 경우나 열처리재의 접합에서는 접합부의 강도가 낮거나 균열이 잘 생기므로 P1을 작게, 가열시간을 길게 하여 Burr를 크게 생성시켜서 접합부의 금속간화합물을 제거하고 급냉을 피하며경화부를 배제하여 우수한 품질을 확보함.* 회전수 : 최대 원주속도 1-5m/sec. Low-마찰토크 불균일, High-과열
(3) 종 류

(4) 특 징
1) 접합에 필요한 입력이 다른 용접법에 비해 매우 작다. 예를 들면 저항용접의 약 1/5~1/10 정도이다.
2) 장치의 자동화하기 쉽고, 대량생산에 적합하다.
3) 용접부의 성능에 영향을 미치는 요인수가 적다. 또한 이들 요인들의 제어가 용이하기 때문에 이음매의 품질 관리면에서 유리하다.
4) 치수 정밀도가 높은 제품이 제작될 수 있다.
5) 이종재료의 용접에서는 압접법 등에서 발생되기 쉬운 취약한 합금 또는 금속간 화합물의 형성이 억제 될 수 있다.
6) 용접시에 아크 등이 발생하지 않기 때문에, 양호한 작업환경이 유지된다.
그러나, 너무 긴 것이나, 용접부에 회전마찰을 일으킬 수 엇는 것, 또는 중량이 큰 것끼리를 용접하는 것은 곤란하다.
초음파 용접
* 초음파 용접법 : 가압상태에서 접합계면에 초음파 진동으로 마찰하면서 가열하여 양쪽 표면의 산화물을 제거하고 더욱 고온으로 되면 두 금속 표면이 밀착하게 되어 원자간의 고상 확산접합이 되도록 하는 용접법.
![]() | |
<그림1> Power source | <그림2> Welding head |
![]() |
<그림3> 초음파 용접 장치의 구성도 |
![]() |
<그림4> 초음파 용접에 의하여 생산한 전자부품과 태양열 집열판의 외관 |
고온 압접법은 가열원으로서 가스 화염을 이용하는 압접법으로 클로즈(close) 법과 오픈(open) 법이 있다.
클로즈 법은 미리 형상가공된 접합단면을 가압한 상태에서 접합부에 온도가 균일하게 되도록 주위로부터 다공식의 링 버너(ring burner)로 가열하여 압접하는 방식이다. 화염으로서는 화염의 성질 조성이 쉬우며, 안정된 고온을 얻을 수 있는 산소-아세틸렌 염이 사용된다.
오픈 법은 처음에는 접합단면을 분리한 상태에서 가열하여, 균일하게 얇은 층만이 용융되었을 때 버너를 빼내고, 급속히 가압하여 용융금속을 밀어 붙여 접합하는 방식이다.
클로즈 법의 접합기구에는 몇 개의 說이 있으나, 가열에 따르는 표면에너지의 증대 혹은 소성변형능의 증가에 의해 금속 접촉면적이 증가하며, 더욱이 원자의 확산 및 재결정 현상이 첨가되어, 견고한 접합상태에 도달하고 있는 것으로 이해되고 있다. 또한 양호한 용접조건에서는 접합단면에 존재해 있던 산화물의 대부분은 상기의 용접과정에서 모재 중에 확산 내지는 미세한 형태로 응집한다. 이와 같은 기구에 의하기 때문에 용접재 단면의 전가공은 중요하며 단면 간의 밀착정도, 면의 다듬질, 녹 및 유지 등의 제거는 용접품질에 커다란 영향을 미친다.오픈 법에서는 플래시 용접 등과 같이 접합단면에 형성시킨 용융층 간을 눌러 붙여 확실한 일체화를 도모하는 것이다. 이 경우 용융 표면에 존재했던 슬래그를 배제하기 위해, 이것을 용융금속과 함께 밀어내는 조작을 가하지만, 간편한 가압장치에서는 용융부의 압출이 완전히 이루어지기 어렵기 때문에, 개재물이 남아있을 가능성이 높다. 또한 클로즈법에 비하여 가열온도가 높기 때문에 접합부에 과열조직이 생기기 쉬운 단점도 있다.
11.폭발용접(爆發熔接; explosive welding)
(1) 원 리
그림과 같이 화약의 폭발압력에 의하여 2개의 금속판을 접합하는 방법이며, 다른 고상용접에서와 같이 이종재(異種材)도 용접이 된다. 일반적으로 부식저항이 큰 판을 base metal에 접합하거나, 큰 면적의 접합을 요할 때 적용되며, 접합부에 있던 표면막은 액체가 되어 밀려 나온다. 이 용접법에는 경사법(傾斜法)과 평행법(平行法)이 있으며, 경사법에서는 상판(上板)을 3 ~ 30o로 경사시키고 그 위에있는 폭약을 뇌관을 통해 점화시키면 폭발압력에 의한 충격에 의하여 소성변형을 하면서 압접된다. 평행법에서는 2판의 적당한 간격에서 경사법에서와 같은 방법으로 폭발시키면 된다. 폭발용접의 특징은 다음과 같다.
(2) 장점 및 단점
1) 장 점
a. 이종금속을 포함한 다른 방법으로 용접이 어려운 재료의 용접을 할 수 있다.
b. 접합강도가 크다.
c. 6m * 2m 정도의 큰 면적의 용접도 할 수 있다.
2) 단 점
a. 취급에 위험이 따르므로 훈련된 기술자가 필요하다.
'건축' 카테고리의 다른 글
한국철강협회 ‘내지진 강관구조’발간 (0) | 2011.05.05 |
---|---|
턴버클 (0) | 2011.04.06 |
구조설계_마찰접합용 고장력 볼트 (1) | 2011.04.04 |
스텐레스재료규격 목록 (0) | 2011.03.18 |
각파이프, 원형파이프 규격 (0) | 2011.03.18 |